What Makes Cinder Blocks Different
Concrete blocks and cinder blocks, as well as split face blocks and lightweight blocks, are all referred to as CMUs (concrete masonry units). CMUs are used for the construction of load-bearing foundation walls, basement walls, partition walls, exterior walls, retaining walls, and non-load-bearing partition walls. Employing reinforcement bars and filling the hollow cores with concrete results in strong structural walls. CMUs may look similar, but there are big differences among them!
Standard (high-density) concrete blocks are made from cast concrete – Portland cement, sand, and gravel. Compared to typical structural concrete, they are made with a higher percentage of sand and a lower percentage of gravel and water for a stiffer mixture that holds its shape when removed from the block mold. The typical high-density concrete block (8 x 8 x 16 inches with two cores) weighs 36-42 lbs. per block.
Lower-density blocks may use industrial wastes, such as fly ash or bottom ash as an aggregate instead of the sand or fine gravel used to make true concrete.
“Cinder block” is an archaic term from the time when power plants and coke ovens in steel mills produced huge amounts of “cinders” from burning coal. They were patented back in 1917. Modern cinder blocks are usually made with volcanic pumice instead of cinder unless there is a nearby coal-fired power station or cement kiln to supply pulverized cinders or fly ash.
There are builders that prefer cinder blocks because they are much easier to work with. Compared to a heavyweight concrete block, a typical cinder block weighs only 26-33 lbs. However, cinder blocks are more subject to moisture, water seepage, radon gas, salt deposits, and efflorescence (white powdery residue) problems because of their high porosity. This is why they are often used in interior non-moisture construction or outdoors for barrier walls, hardscapes, and fences.
- Lightweight CMUs – Gravel is replaced with shale or clay expanded at extreme temperatures which makes the blocks much lighter at 22 to 28 lbs. each.
- Split-faced Blocks – Have a rough, stone-like texture on one face of the block instead of a smooth face.
- Haydite Blocks – Another example of an expanded shale product. Lightweight blocks cannot be used in retaining walls or exterior building walls because they readily seep water.
Why Cinder Block Basement Walls Leak Water
A cinder block is significantly more porous compared to standard concrete blocks and poured concrete. Cinder blocks are classified as permeable to water and water vapor (+10 perms). Heavyweight concrete blocks are semi-permeable (5 perms) and less so when the hollow cores are filled and packed with a slurry mix of concrete (about two perms). High-quality, newly poured concrete foundation walls (8-10″ in thickness) are impermeable to water (0.4-0.3 perms).
Making matters worse, only a thin wall (1-3/4 inch) separates the hollow cores of the cinder block from filling up with water and leaching out. Damp cinder block walls are frequently noticeable after inclement weather conditions; wind-driven rains, heavy rainfalls, water-soaked ground, saturated zones, and high-water table areas. When the hollow cores of the blocks retain groundwater, the thin walls offer little resistance against hydrostatic water pressure, and the cinder blocks dampen and leak. Water can easily pass through the cracks in the mortar joints and leach through the capillaries and pores, causing basement walls to dampen.
If you have a wet basement constructed with cinder blocks, they are more likely to leak water compared to poured concrete foundation walls. It may take a number of years, but once the exterior waterproofing coatings and damp-proofing membranes deteriorate, the cinder blocks will be on their own to fight against negative side water pressure. It can be a losing battle because cinder blocks are water-permeable!
Exterior, above-grade cinder block walls (retaining walls, decorative walls) are not often subject to hydrostatic water pressure complications. However, during periods of wind-driven rain, water will be easily absorbed into porous surfaces, increasing the chances of surface efflorescence and lime staining.
Applying a Concrete Sealer Is Important
Prevention of water is much easier and cheaper than the cure! If you avoid sealing foundation cinder blocks before water issues start, they can and may become unsealable in the future.
How It Begins
• Efflorescence will loosen and leach from within the matrix of the cinder block, being the first sign that water is present inside the hollow cores. Years of continuous water seepage and purging efflorescence will further enlarge the pores and capillaries of the blocks.
• Next, the blocks will begin appearing wet, and more often so, during inclement weather conditions. Allowing years of water seepage through the foundation CMU walls can create pinholes. Pinholes allow the water to percolate through the thin facade walls and run down the inside of the basement wall.
• In severe cases, the hollow cores fill with water, and the cinder blocks leak water, like turning on a faucet, wetting, and puddling on the basement floor.
By sealing cinder blocks early on, you can help further waterproof the blocks. It will extend their life by protecting them against water and efflorescence, the main enemy of concrete.
• In rare cases, extensive water seepage can carry soil and silt through the concrete block and begin to plug the pores. Making the cinder blocks almost impossible for waterproofing sealers and waterproofing paints/coatings to waterproof the substrate. The telltale sign of soil buildup within the matrix of the blocks would be a “brown or reddish” color to the interior surface of the wall.
Blocks that have become unsealable from the inside/out with penetrating sealers, waterproofing paints, cementitious skim coatings, and rubberized membranes will require expensive exterior solutions by basement waterproofing companies. There is no cure!
Did You Know? Some cinder blocks release mercury and other heavy metal contaminants which is another reason for sealing them. • Coal Combustion and Gasification Products (CCGP)
RadonSeal Plus + Ion-Bond Armor
__________
Use RadonSeal Plus followed by Ion-Bond Armor for sealing basement cinder block walls that routinely dampen and purge efflorescence during periods of excessive ground saturation and heavy rainfalls.
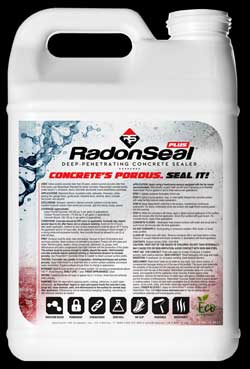
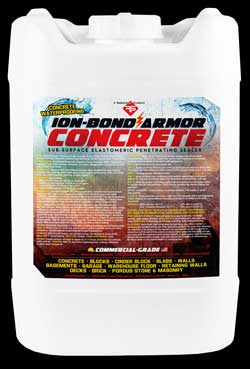
How To Waterproof Your Cinder Block Foundation Walls
Use RadonSeal Plus + Ion-Bond Armor
To aid in waterproofing, strengthening, and preserving the overall appearance of your cinder block foundation walls, seal the blocks permanently against moisture, water vapor, and efflorescence with RadonSeal Plus Penetrating Concrete Sealer.
RadonSeal is the strongest, penetrating concrete sealer for blocking water vapor and capillary water seepage through concrete and concrete blocks. RadonSeal is recommended for use on below-grade and slab-on-grade concrete applications because it is permanent and 100% resistant to hydrostatic water pressure.
While RadonSeal Plus alone can successfully seal the majority of basement cinder block walls, there is a possibility it may not entirely suffice for waterproofing all cinder blocks. The reason why is that RadonSeal works by reacting with cement, lime, and alkali. Cinder blocks use industrial wastes, such as fly ash or bottom ash, as an aggregate instead of the sand or fine gravel used to make concrete. Making sealing cinder blocks much more challenging! The combination of applying RadonSeal Plus and Ion-Bond Armor is the tightest seal against water seepage and is often required for challenging situations.
Follow these steps to help prevent basement water seepage through newly constructed concrete block walls and cinder blocks that have leaked previously in the past:
- Remove Paint and Efflorescence – In order for the blocks to absorb the concrete sealers, the surface must be bare and porous. Remove previously applied waterproofing paints mechanically (wire brushing, grinding, sand-blasting) or use chemical paint strippers and scrape them off. Light amounts of efflorescence buildup can be removed with wire brushes or a wire-wheel attachment. To best remove efflorescence, use RadonSeal Efflorescence Cleaner.
- Allow the Cinder Block Walls To Dry Out – RadonSeal Plus cannot react if the hollow cores and the pores of the blocks are saturated with groundwater. If the foundation wall is visually damp, allow them to dry out thoroughly! To help speed up drying time, ventilate your basement or garage by opening windows and doors. Install a fan to improve airflow. If the blocks are continuously wet, drill weeping holes using a masonry drill bit at the bottom of each core
- Apply RadonSeal Plus – Spray TWO wet-on-wet applications of RadonSeal Plus at a coverage rate of 200 sq. ft. per/gal (coverage rate takes into account both applications).
- Apply Ion-Bond Armor (recommended) – Allow RadonSeal to cure inside the concrete for 7-10 days. Afterward, apply a saturating application of Ion-Bond Armor Subsurface Elastomeric Concrete Sealer at a coverage rate of 100-150 sq. ft. per/gal.
Ion-Bond Armor is a self-reacting penetrating concrete sealer, which will also disappear into the concrete, where it bonds and internally cures to seal the concrete even tighter. For more porous concrete like cinder blocks, we strongly recommend using Ion-Bond Armor as the second cinder block sealer.
Hard To Seal CMU Walls
Applying RadonSeal Plus and Ion-Bond Armor is the best concrete block sealer for use on cinder blocks foundation walls. The combination of the two concrete sealers has proven to be foolproof for many frustrated homeowners dealing with damp basements. Truth be told, older cinder blocks and sandstone foundations, that have been exposed to decades of water seepage, may require special steps to properly fill and seal the enlarged pores and pinholes.
Many different types of concrete blocks vary widely by composition, additives, region, and manufacturer. Since RadonSeal Plus seals concrete by reacting with Portland cement, it simply can not be guaranteed to seal all blocks with little to no cement content. With that said, ALL waterproofing sealers, concrete paints, and coatings will have difficulty sealing blocks with unusually large pores.
- Lightweight Blocks – Split face, haydite, and dry-pressed blocks (all being much lighter than the 38 lbs. of standard concrete blocks). They can be sealed and waterproofed with our LastiSeal Brick & Concrete Sealer or DryWay Water-Repellent Concrete Sealer.
- Popcorn Blocks – Made with a very coarse aggregate with large toothpick-size holes. Use LastiSeal Brick & Concrete Sealer or DryWay Water-Repellent Concrete Sealer.
RadonSeal Plus + Thin-Set + Ion-Bond Armor
__________
Apply RadonSeal Plus. Skim coat the cinder blocks with thin-set mortar. Apply Ion-Bond Armor over the thin-set. Used for harder to seal cinder block walls that historically get wet (or seep water) after heavy rainfalls and.
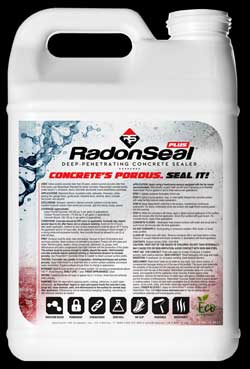
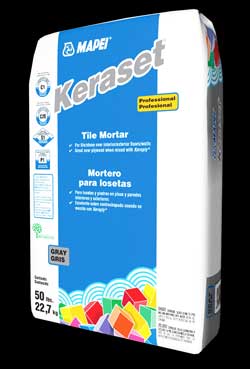
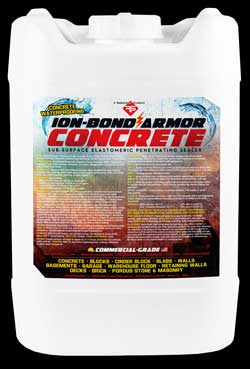
The Thinset Mortar Method for Damp Basement Walls
Use RadonSeal Plus + Thinset + Ion-Bond Armor
An option proved successful in many hopeless situations!
- Purchase Thinset Mortar – Quality thin-set mortar (without vinyl additives) is available in most home improvement stores.
- Use RadonSeal Plus and Apply the Mortar to the Cinder Blocks – Apply two wetting applications of RadonSeal Plus to the blocks. After applying RadonSeal, use the smooth edge of a 3/16″ notched trowel holding it at a 45° angle, and apply a skim coat of the mortar over the surface of the cinder blocks. Push the mortar into the rough-textured areas. The goal of using thin-set mortar is to fill any enlarged pores and pinholes of the cinder blocks. Repair any mortar cracks and separations in vertical and horizontal joints.
- Tip – Skim coating can be a messy job. There will be lots of mortar droppings on the ground. Finish it off neatly by going over the mortar joint with a tucking tool. It will appear like it is a brand-new wall when finished. If you prefer the look of poured concrete, leave a smooth 1/8″ layer on the surface.
- Seal the Mortar Using Ion-Bond Armor – Thin-set is porous and can dampen when the block gets wet again. Allow 4+ days for the mortar to cure, then seal over the thin-set with Ion-Bond Armor. Ion-Bond will penetrate through the thin-set, bond with RadonSeal, and further waterproof the cinder blocks and the mortar joints.
The ElastiPoxy Method for Cinder Block Walls
A more resistant alternative to using thinset mortar is to skim-coat the cinder block foundation walls using our ElastiPoxy Joint & Crack Filler Kit. When mixed with sand, ElastiPoxy cures as a hard coating that will provide a waterproofing barrier against negative side water pressure. This method is particularly useful on dilapidated and crumbling cinder block foundation walls that leak like a sieve.
- Apply RadonSeal Plus – Apply two wet-on-wet applications of RadonSeal to help seal the pores of the blocks.
- Apply ElastiPoxy Joint & Crack Filler Kit – Mix ElastiPoxy with dry construction sand and use a trowel to push the mixture into the pores of the blocks. Use also to repair and fill cracks, holes, and softened mortar joints. The epoxy-sand mix delivers a repair that is stronger than the concrete itself. It will last forever!