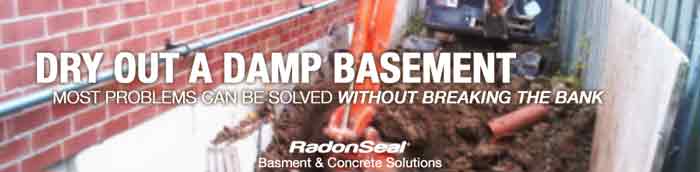
That Damp Basement Feeling
Does your basement just feel damp? Does it have a musty smell? Do cardboard boxes get wet when placed on the concrete floor? Is the concrete wet when you lift rubber-backed carpeting or a mat? Do you see signs of efflorescence on the basement walls or floor?
If this all sounds too familiar then you likely are one of the 60% of homeowners dealing with a damp basement. Dampness and high humidity causes mold and mildew growth, musty smells, damages furnishings (possibly damaging the structure itself), buckle wood flooring on slab-on-grade foundations, and most importantly is hazardous to people’s health.
Moisture insulation does not work well and high humidity is more costly to heat or air condition. A damp basement will also increase your heating and air-conditioning bills. If this all sounds too familiar then you likely are one of the 60% of homeowners dealing with a musty basement! It is best to fix the problem sooner than later before it causes serious damage to your home and bank account.
Moisture Migration Through Concrete
The pores in concrete allow groundwater to be pushed by hydrostatic pressure and also actively draw in water by wicking (capillary action). The water usually quickly evaporates as invisible vapor, releasing water vapor and radon. It leaves behind dissolved minerals – efflorescence (“white powder”) which is the telltale sign of capillary water seepage.
Moisture-laden soil gas is pulled in from the ground through openings and pores in concrete by the difference in air pressure and just like gases, water vapor moves by diffusion to a space with lower relative humidity. The water molecules are pulled in by a “vapor drive.” The relative humidity of soil gas is close to 100%, much higher than in the basement. The vapor pressure in the ground is often twice the vapor pressure in the basement.
Your basement or slab-on-grade is the single largest source of humidity in your home.
The average basement lets in 15–18 gallons of moisture each day, several times more than showering, laundering and cooking combined (3–5 gallons/day). In case of slab-on-grade construction, moisture migration through the concrete slab may amount to 12 gallons per day. For more on indoor air pollution, molds, mildew, dust mites, and their health effects, please read Indoor Air Quality and Moisture.
Vapor Barriers Under Concrete Slabs
Floor slabs let in much more water vapor than poured walls – Concrete slabs are only half the thickness and much more porous because they are cured on a plastic sheet (all surplus water moves to the surface). Usually, polyethylene sheets 6 mil (0.15 mm) thick placed on a gravel bed before pouring a concrete slab. They are more correctly called “vapor retarders” because they are not fully impermeable to water vapor (around 0.1 perms).
Many sheets are now made of recycled rather than virgin materials and are much more permeable to vapor. Their quality is dubious and there is no permeance standard – any plastic sheet will do.
In real life, they do not provide much protection. They get punctured or torn during installation or the seams are not properly joined. And it is almost impossible to seal the sheet around all the floor penetrations like drains, drain trenches, electrical ductwork, conduit, and plumbing. Worse yet, lime in the concrete breaks down the polyethylene after several years.
There are high-quality vapor retarders available, guaranteed for 10 or even 15 years. But the best solution is assuring that your slab has low porosity:
- QUALITY CONCRETE – Good-quality concrete with low water/cement ratio.
- CURING TIME – Extended moist-curing to reduce porosity and cracking.
- DEEP-SEALING – Strengthening the concrete with RadonSeal® Permanent Concrete Sealer.
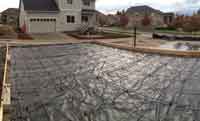
Damp Proofing or Waterproofing Foundation Walls?
What’s The Difference? – There is a big difference between damp proofing and waterproofing. By definition, damp proofing is supposed to retard moisture but, unlike waterproofing, it does not have to stop hydrostatic water pressure.
The ol’ “black stuff in a bucket” is just hot liquid asphalt originally created for road repair. Nowadays, it is water-based. The thickness of the bituminous tar is not specified – it is only 10 mils thick at most when cured. It soon disintegrates due to the “alkali attack” from concrete – its life expectancy is between 18 months and 3 years.
The tar damp proofing is inexpensive and meets the lowest minimum standard. Most building codes require that “unfinished” basement living spaces only be damp-proofed (no guidance on what to do if you later finish the basement). The codes usually also require that if masonry walls enclose a habitable space, they must be first covered with 3/8 inch thick parging made of Portland cement.
Damp proofing may be acceptable if there is a sandy soil and great drainage. But often, there is a high water table or poor soil. Clay holds rainwater, which builds up hydrostatic pressure against the foundation. Moreover, water cannot drain through the undisturbed soil under the footings and groundwater level rises.
Degradation of Damp Proofing Coatings
The exterior tar coating is not flexible, nor is parging on masonry walls. It cracks as the concrete continuously expands and shrinks, and as the house settles. Once it cracks, water gets into the concrete and leaches out lime, which disintegrates the coating by “alkali attack.” In moist conditions, it may last just a couple years.
Elastomeric membranes last much longer. Most spray coatings are in the range of 30 mils to 60 mils wet application and a dry film thickness after curing of 15 mils and up. But the spray-on membrane may not be sprayed on evenly. Sheet membranes (60 mils thick) are put on like wallpaper but are joined with a tape and depend on a primer. These are the weak points susceptible to “alkali attack” from the concrete. The membranes are usually not guaranteed for longer than 5 or 10 years.
The polyethylene “vapor barrier” under the slab disintegrates quickly due to the lime in concrete. But this does not make much difference because it already has holes and tears from installation.
When exposed to lots of water, there is little exterior protection left and the concrete is on its own after 5 or 10 years. Then, the dry basement and healthy home depend on the density and porosity of the concrete. Ideally, the concrete has been sealed with RadonSeal.
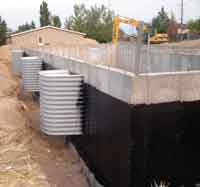
Good Damp Proofing Can’t Be Beat!
Good waterproofing is a wise investment. It is not just a coating but a whole system that includes:
- Spray-on or roll-on rubberized membrane (or tar and a polyethylene sheet),
- Drainage/protection/insulation layer (gravel, mats, beadboard),
- Foundation drainage system (footing tiles).
An air gap membrane is a thick, dimpled, high-density polyethylene sheet that is unrolled horizontally along the foundation wall and then mechanically fastened. Any water will quickly flow down to the footing drain. They can easily bridge a 1/4-inch crack and resist alkalis. Some are less expensive than elastomeric membranes. But no matter what you have on the walls, water may come up through the floor!
How To Dry Out a Damp Basement
Divert rainwater from the foundation by proper grading, gutters, and downspout extensions. Seal all cracks and openings. Make sure that your clothes dryer is exhausted to the outside and the duct is not plugged up by lint. When finishing the basement, avoid trapping moisture behind plastic sheets, impermeable wall or flooring materials and/or provide ventilation for water vapor seeping through concrete.
- Air-Conditioning
- It will remove some humidity but not enough. It shuts off when it reaches the target temperature regardless of humidity. Still, a full 30% of an air conditioner’s load is used to remove humidity. By reducing indoor air humidity, you will save on air conditioning bills.
- Dehumidifier
- The most common solution. Power consumption $30-50/month. Be sure to keep it clean to avoid mold growth, which would defeat its purpose. It draws in 20 to 30% more moisture through the concrete, which in the long run speeds up its deterioration and allows in more moisture.
- Air-To-Air Exchanger
- Pulls out humid air from the basement and draws in fresh air from the outside. Unlike just openings the windows, the exchanger reduces the energy losses in heated or air-conditioned air. In general, a good solution for today’s “airtight homes” with low fresh air exchange. But rather costly initial cost and operation.
- Seal the Concrete
- The most basic, least expensive, and effective methods with no on-going running costs. Seal the concrete walls and floor with RadonSeal® Deep-Penetrating Concrete Sealer to greatly reduce the transmission of water vapor, seepage, and radon gas.
- Repair Cracks, Seal Gaps
- Seal all openings or gaps in the concrete that easily allow water vapor to pass through. Repair concrete cracks in foundation walls using our DIY Homeowner Crack Injection Kits.
Read Customers’ feedback and tips on Sealing Damp Basements
RadonSeal Damp Proofing Products
- RadonSeal® Deep-Penetrating Concrete Sealer
- Penetrates up to 4″ into concrete, chemically reacts with lime and alkalis, expands and hardens as a cementitious minerals. Seals concrete against liquids and gases like water vapor, soil gas or radon. Use good waterproofing on the exterior and seal the concrete inside RadonSeal®.
- Ion-Bond Armor Concrete Sealer
- Forms a subsurface water-repellent membrane. Does not depend on the cement content of concrete. Use on concrete with lower cement content, such as rat slabs, thin concrete, cinder blocks, or fibercrete.Or use it after RadonSeal® – the combination of the two provides the lowest possible vapor transmission rate through concrete.
- Do-It-Yourself – Homeowner Crack Injection Kits
- Easily, and permanently repair cracks in poured concrete walls with expanding polyurethane polymer.
- BioZap Air Purifier & Deodorizer
- Prevention or control of musty odor from mold. The natural air cleaner – releases the vapor of Australian tee tree, which kills molds, mildew, spores, and bacteria in the air or on surfaces.
Read Customers’ feedback and tips on Waterproofing Wet Basements
Condensation in Damp Basements
When humid air is next to a cold surface, its temperature may drop below the dew point. Its relative humidity rises to 100% and it sheds the excessive humidity by condensation.
The ground temperature is typically 52 to 55°F. Heated air in the basement keeps concrete surfaces warm. But if you put a carpet on the floor, it insulates the concrete and its surface receives less heat from the indoor air and becomes colder. If the air in the basement is humid, the air temperature in the microclimate under the carpet (or behind a wall) will drop below the dew point.
Water Gets into Basements Three Basic Ways:
- CRACKS – Leakage through cracks and openings
- CONCRETE – Direct water seepage through concrete
- CONDENSATION
Insulate cold air-conditioning ducts. Excessive moisture may condense on cold windows. But the real problem may be the condensation you do not see – behind basement walls or underneath the flooring. Trapped moisture from vapor transmission and condensation leaches out lime, which disintegrate adhesives, padding, and even the flooring itself.
What is the Right Humidity Level for a Basement?
Molds, mildew, dust mites, and other biological contaminants need moisture to grow. Depending on the type, they thrive in relative humidity above 50 or 60%, or as low as 45%. It is more difficult to keep the humidity low in humid summer weather.
The Recommended Target is 30% Relative Humidity in Winter and 50% in Summer.
To measure humidity, you can purchase an inexpensive hygrometer. For more on controlling molds and mildew, toxic black mold, and their health effects visit Molds and Mildew Solutions.
Permeance of Building Materials
Permeance characterizes how easily water vapor diffuses through a material – the lower, the more resistance to vapor migration. Permeance is measured in perms (grains/ hr-sq. ft.-inch Hg), i.e. water vapor transmission rate (grains/hr-sq.ft.) per unit of pressure differential (inch Hg). (1 perm = 1.47 ng/sec-sq.m-Pa). Avoid trapping water vapor, condensation, and molds behind walls in finished basements and under the floor covering on a concrete slab. General classes of materials by permeance and examples:
Vapor Impermeable – 1.0 perms of less:
- Elastomeric or bitumen membranes (0.05–0.5 perms)
- Polyethylene film (0.1 perms)
- Foil-faced insulation
- Ceramic tiles (but not grout), VCT tiles, linoleum
- Epoxy, heavy urethane or oil-based paints
- Vinyl wallpaper
Semi-Permeable to Vapor – 1 to 10 perms:
- Unfaced expanded or extruded polystyrene (2 or 1.2 perms/inch)
- Heavy asphalt impregnated building papers
- Fiberglass batt insulation with paper or bitumen facing
- Plywood, OSB
- Gypsum board painted with latex paint
Permeable to Vapor – over 10 perms:
- Unpainted stucco or plaster
- Unfaced fiberglass insulation, cellulose insulation
- Cementitious waterproofing coatings (20 perms)
- Interior waterproofing paints
- Lightweight asphalt impregnated building papers
- House wraps
- Unpainted gypsum wallboards (50 perms).
Vapor Permeability of Concrete
How about the permeance of concrete? According to ASHRAE Handbook, the permeance of concrete (1:2:4 mix) is 3.2 perms per inch of thickness. Then, a 4-inch slab would have (3.2/4=) 0.8 perms. But this is only for “good quality” moist-cured concrete with low water/cement ratio. Most basement slabs are much more porous. Although they may be almost impermeable to water, basement slabs are semi-permeable to water vapor (>1 perm).
Newly poured concrete walls are classified as impermeable to vapor (8–10 inches thick, 3.2/8 = 0.4 perms for good quality concrete). However, once the exterior waterproofing coating disintegrates, water starts enlarging the pores in concrete and the walls will become permeable and later, may even start seeping water. Walls made of pre-cast panels have the lowest permeance because they are made of high-strength concrete under controlled factory conditions.
Hollow concrete blocks are a different story. They have only a 1 1/4-inch wall outside the hollow cores (3.2/1.25 = 2.6 perms). The concrete is very porous and the hollow cores fill up with water vapor, which then moves to the most permeable area to get indoors. The porosity of blocks varies widely. Some tests of good concrete blocks show 2.4 perms when the cores are filled or 4.8 perms for hollow blocks. Hollow concrete blocks are semi-permeable (say 5 perms) but lightweight CMUs, splitface blocks, “popcorn” blocks, and cinder blocks are permeable (>10 perms).
If possible, use poured concrete instead of standard blocks (concrete masonry units – CMUs) for foundations. Or make at least sure that the hollow cores are properly filled during construction. Apply parging on the exterior and a good waterproofing coating. Concrete block walls are also less able to resist lateral pressure of water and earth – high clay soil or expandable clay can cause structural damage.
Infiltration of Soil Gas and Pesticides
How about the permeance of concrete? According to ASHRAE Handbook, the permeance of concrete (1:2:4 mix) is 3.2 perms per inch of thickness. Then, a 4-inch slab would have (3.2/4=) 0.8 perms. But this is only for “good quality” moist-cured concrete with low water/cement ratio. Most basement slabs are much more porous. Although they may be almost impermeable to water, basement slabs are semi-permeable to water vapor (>1 perm).
Newly poured concrete walls are classified as impermeable to vapor (8–10 inches thick, 3.2/8 = 0.4 perms for good quality concrete). However, once the exterior waterproofing coating disintegrates, water starts enlarging the pores in concrete and the walls will become permeable and later, may even start seeping water. Walls made of pre-cast panels have the lowest permeance because they are made of high-strength concrete under controlled factory conditions.
Hollow concrete blocks are a different story. They have only a 1 1/4-inch wall outside the hollow cores (3.2/1.25 = 2.6 perms). The concrete is very porous and the hollow cores fill up with water vapor, which then moves to the most permeable area to get indoors. The porosity of blocks varies widely. Some tests of good concrete blocks show 2.4 perms when the cores are filled or 4.8 perms for hollow blocks. Hollow concrete blocks are semi-permeable (say 5 perms) but lightweight CMUs, splitface blocks, “popcorn” blocks, and cinder blocks are permeable (>10 perms).
If possible, use poured concrete instead of standard blocks (concrete masonry units – CMUs) for foundations. Or make at least sure that the hollow cores are properly filled during construction. Apply parging on the exterior and a good waterproofing coating. Concrete block walls are also less able to resist lateral pressure of water and earth – high clay soil or expandable clay can cause structural damage.